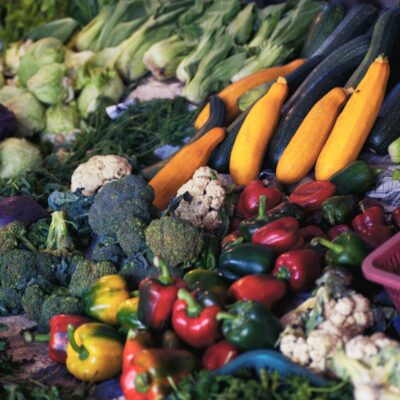
What are the biggest challenges of food retailers when it comes to food safety?
The way the food retail industry operates almost resembles a spider web, facing numerous challenges that continually test its resilience. This web is made up of multiple interconnected elements, including suppliers, producers, logistic partners, transportation and distribution networks, enforcement authorities, and finally the reputation of the products on store shelves. While each of these elements present their own unique challenges, the approach to addressing them all remains consistent: the commitment to keeping consumers safe.
Compartmentalization of Information
Similar to how the spider’s web strength comes from the connection of its threads, seamless information flow between different departments and stakeholders is crucial for the effectiveness of food retail operations. Thinking of the food retail industry like a spider’s web, serves as a metaphor to allow us to understand better why one of the most important challenges that this industry faces, is the compartmentalization of information.
Often this is expected due to the inherent complexity of the food retail business model together with the big volume of data that needs to be assessed and managed. But working silos make it challenging for different departments to share real time information effectively and can impede the swift removal of unsafe products from the store shelves. A dynamic, centralized platform could offer the needed space where real time information can reach all relevant parties, meaning that cross-departmental collaboration is enhanced.
The dual role of retail companies
Unlike most food manufacturing companies that focus solely on production, most major retailers wear two hats. They act as ‘creators’ developing their own brand label products, but they also serve as ‘curators’ selling on their shelves products from established popular brands. This dual role poses a unique challenge, as retailers not only must maintain the safety and quality of their own brand products, but they must also safeguard their reputation as ‘gatekeepers’ of other brands. Dynamic risk prioritization is therefore crucial, not only in ensuring compliance but as a proactive strategy to stay one step ahead of possible food safety crisis involving both own label and branded products.
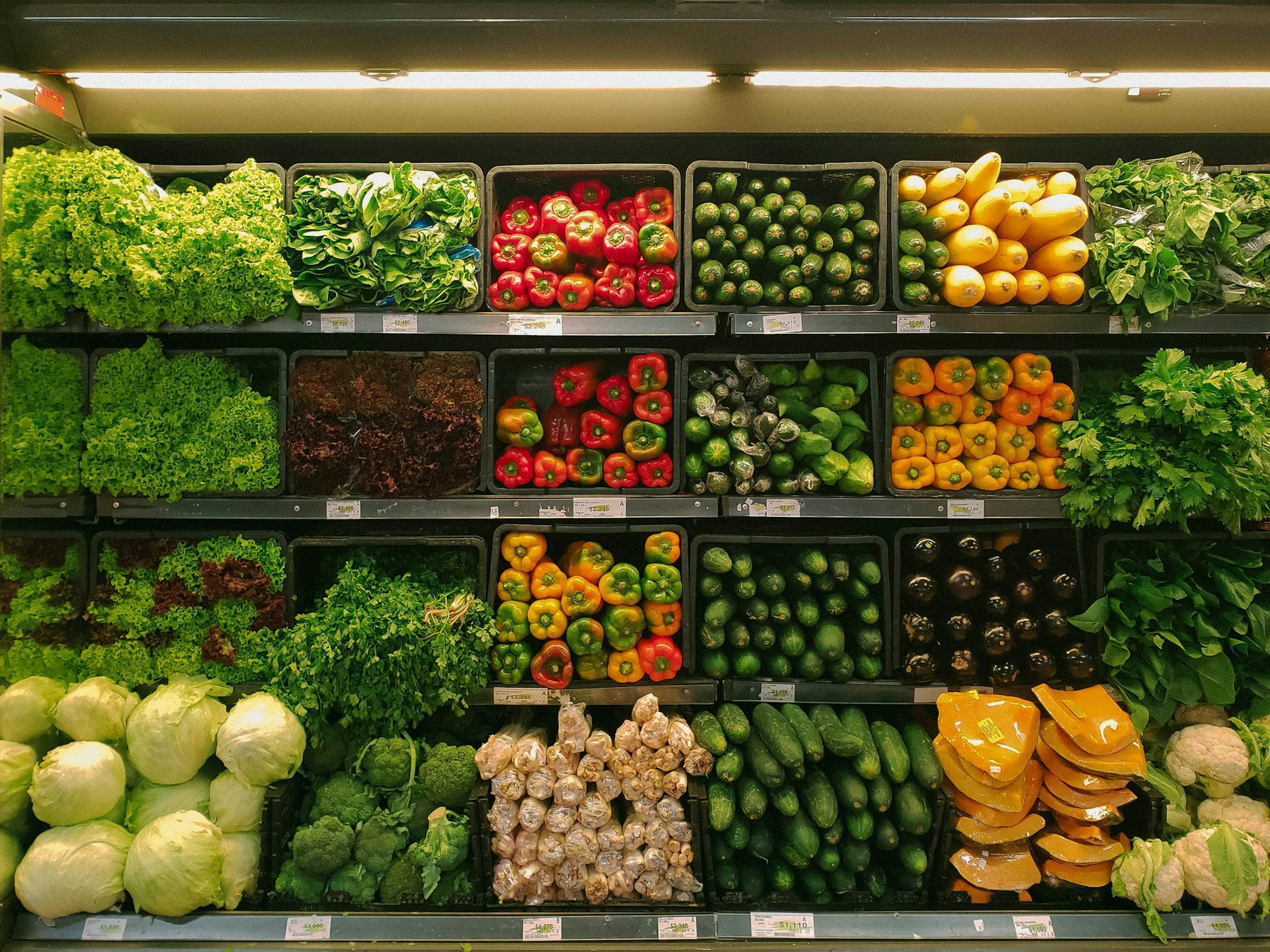
The vast number of suppliers
The major players in the retail industry are dealing not just with hundreds, but potentially thousands of suppliers located all around the world and spanning through different and diverse product categories. From ready meals, to dairy, to produce, and more, each category comes with its own set of regulations and legislations. To complicate matters more, imagine that each country imposes different regulations, and often large retailers have stores in more than one country! Auditing this network of suppliers and continuously monitoring food safety compliance and risk performance is of course a very difficult task that demands great focus. What is even more difficult, however, is to cultivate the type of relationship with the supplier to ensure that open communication is promoted and to prevent crucial information from slipping through. A retailer wouldn’t want to learn about a crisis only from the local authority!
The responsibility to shape the food industry
Major food retailers, however, apart from their obligation to keep consumers safe, are responsible for actively shaping the future of the food industry. They are not just expected, for example, to adhere to regulations but to be a force in molding them. This ‘duty’ affects all aspects of their operation, and it requires consistent efforts in regulatory compliance, sustainability, and innovation and most importantly it requires continuous monitoring of food safety compliance and risk performance – a prerequisite in staying ahead of the curve.
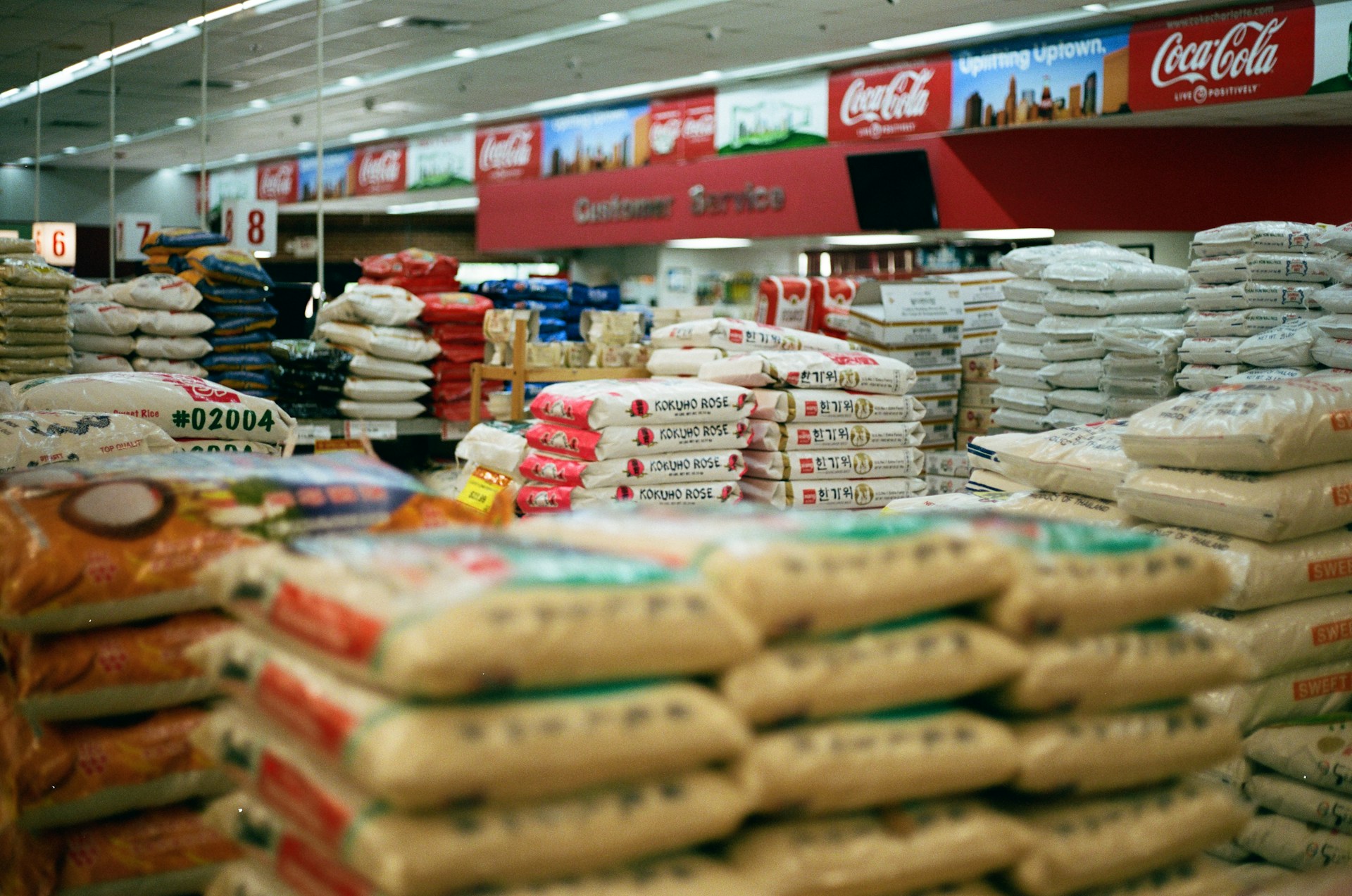
How can a unified risk intelligence platform help tackle these challenges.
Food safety professionals working in the retail industry can observe a high-risk profile associated with one of their suppliers, via FOODAKAI. With real-time insights on the safety profiles of ingredients and finished products, as well as a consolidate view of all news and incidents in the supply chain of sourcing suppliers they could either enhance the controls already in place for that supplier (for example announced audits or scheduled visits and additional testing) or they might even start examining alternate sourcing strategies.
Additionally, in the case of launching a new own label product with the collaboration of an appointed manufacturer, food safety professionals in retail companies can, through FOODAKAI, identify all risks associated with an ingredient that is meant to be part of the recipe for that product. Consequently, they can advise their supplier/manufacturer on choosing an alternative ingredient and strategically guide their sourcing strategy.
FOODAKAI can integrate seamlessly into the day-to-day workflow of retail professionals working in different departments, and to empower them in making informed decisions and staying proactive.
Learn more about how FOODAKAI can elevate critical food risk assessment tasks with a call. Schedule a call here.
Want to receive helpful food safety intelligence in your inbox?
Funding for this research has been provided by the European Union’s Horizon Europe research and innovation programme HOLiFOOD (Grant Agreement Number 101059813). Funded by the European Union. Views and opinions expressed are, however, those of the author(s) only and do not necessarily reflect those of the European Union or European Research Executive Agency. Neither the European Union nor the granting authority can be held responsible for them